导言:
精益管理原则和实践数十年前就开始在国内企业开始引入,甚至有些企业开展精益管理已经超过十年。通常企业会定期开展精益生产培训、推行一系列精益改进项目和选拔管理骨干到精益标杆企业考察学习,企业希望通过这样的开展方式来实现企业绩效和管理能力的提升。然而,许多在中国运营的企业(包括外资企业)到目前为止在推行精益管理方面未能达成预期效果。
企业在开展精益管理工作过程中遇到的困难重重,推行效果也反反复复,企业谈的多真正实施到位的少,以至于有些企业管理人员甚至开始怀疑精益管理不一定适用本公司。
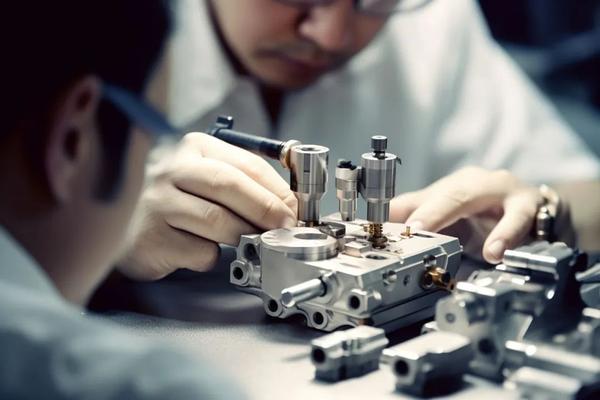
在精益管理推行中我们经常会遇到下列问题:
1. 精益改进项目短期效果显著但缺乏持续性;
2. 生产部门推行精益得不到其他职能部门的配合,推进仅限于生产部门;
3. 中基层管理干部忙于日常救火,对精益改进工作敷衍了事;
4. 一线员工未能从精益改善中获得好处,还是按原有的工作习惯办事;
5. 推行的改善项目众多,但管理层未看到实际的绩效提升和财务收益;
6. 在管理层变更或精益经理离职后,精益推进工作停滞甚至回到解放前;
7. 。。。
企业在精益管理推广过程中遇到的上述种种挫折,其中固然有中国制造业当前所处发展阶段和企业特定的商业环境的原因,但导致企业推行精益未达成预期效果的原因,更多是企业在推进精益管理工作是缺乏系统且改进形式单一所造成。
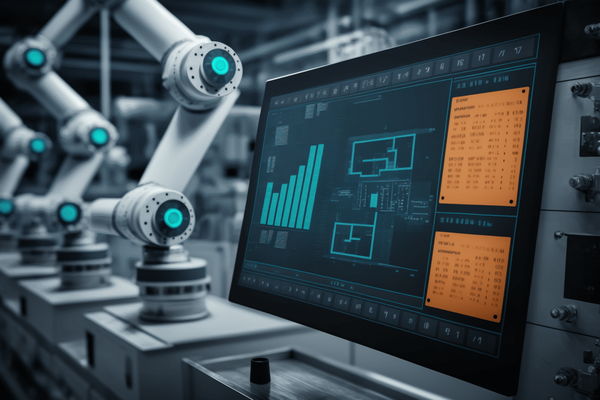
精益推进不仅要改善(Kaizen)还要改恶(Kaiaku)
系统推行精益管理不仅要持续开展改善活动,更重要的是分阶段进行改恶活动,即寻找出导致改善成果倒退原因。改恶是系统性固化成果的精益方法,本质上需要各个层级乃至每一人的参与,只有当改恶的原则和方法内化为组织能力,企业才能从容应对在精益推进过程中遇到的层出不穷的问题和挑战,并能实现自我完善。
为了更好的理解改恶原则和方法,让我们一起来学习下在企业推动精益管理过程中常见的10种改恶现象:
1. 成果回陷(Fall Back)
常见的成果回陷包括已实施的改善项目成果不复存在、已运行的规则未能遵守,如目视管理板没有更新和车间现场5S未按照标准执行等。
2. 量化模糊(Vague Metrics)
改善成果无法反映在公司财务报表内,改善过程缺乏对指标变化的关注,我们得来的财务的金额大都是经过处理过的,并不能真实反映现状。
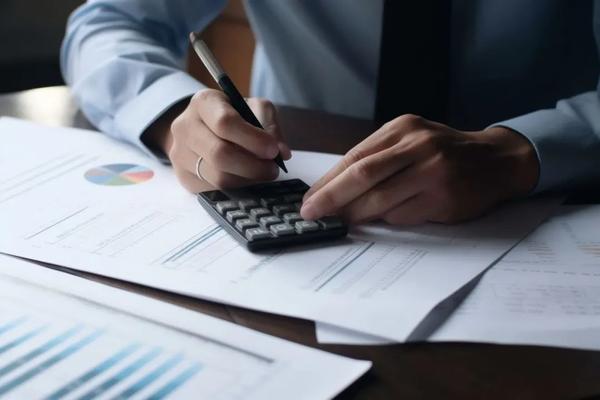
3. 标准虚行(False Standards)
已建立的标准已不复存在,未按设定的标准执行或是在执行过程中不到位。
4. 自我吹嘘(Egotism)
在改善过程中夸大改善成果、把团队的改善成果占为己有、提高自己贬低他人、自我膨胀、拒绝他人帮助。
5. 规而不行(Rules Ignores)
规定的会议、讨论和制度未能及时得以实施。
6. 视而不见(Look vs See)
看到现场异常或不符合标准的事项,不去及时纠正,听任其发生。
7. 四平八稳(Hesitant Actions)
做事有百分百的把握才去做,整体项目进度推进缓慢,缺乏主人翁的精神,未能将工作事情看成自己的事情,对安排的改善跟进工作跟不紧,造成拖期。
8. 为难止步(Fear of Trouble)
行动计划涉及资源较多,不能坚定实施(如跨事业部的项目、购买器具、实现配送、整合供应商等方面,与领导沟通不畅时畏难止步,质量顽疾前畏难止步。
9. 学而不习(Learning vs Practicing)
参加学习后的精益工具并没有能结合项目进行很好的练习,并且没有运用到日常工作中。
10. 似是而非(Make Believe Kaizen)
缺少对现场改善的感觉,内心中没有描绘出一个理想的车间现场;导致项目没有解决根本问题,而出现问题时不能发现并及时解决, 只是初步的实施了项目,而对影响流程的关键行动计划实施不够到位。
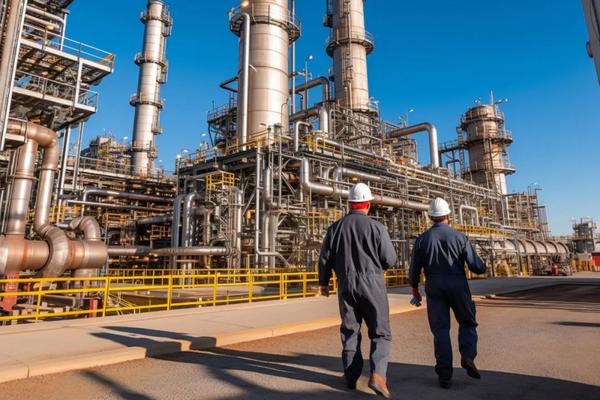
现阶段是中国企业推行精益管理工作已经到了非常关键的时刻,精益推行成果倒退甚至回到解放前水平的现象以成为企业推行精益管理工作的排在第一位的障碍,中国企业需要根据自身的特点来灵活应用精益原则和工具,系统化推进将改善和改恶活动相结合,这样才能找到切合企业自身特点的精益转型之路。