什么是MTBF?
MTBF是Mean Time Between Failure的缩写,意思是两次故障间的平均时间。
那什么是MTTR?
MTTR是 Mean Time To Repair的缩写,意思是从故障发生到保全人员恢复完毕,设备能够正常运转的时间。
MTBF和MTTR这两个指标是设备专业保全部门在设备故障维修工作中所完成的效果和工作效率指标。
分析这两个指标的目的是要掌握在设备保全管理工作的现状和存在的问题点,是为了制定后续工作方针及后续完整的保全计划书,这是预防保养中极重要的数据,也是达到“零故障”的基本分析法。
遗憾的是,这两个这么重要的指标,在很多公司却并未引起大家的注意,也未统计和分析。那么他们为什么重要?怎么分析?
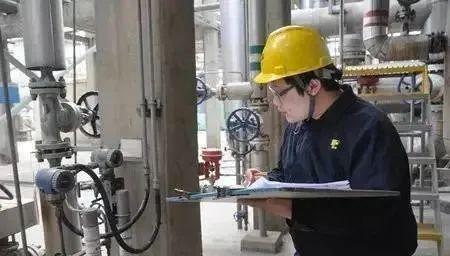
MTBF的计算方法
MTBF是故障平均间隔时间,通俗来讲就是每次故障距离上次故障的平均时间。
按正常来讲,应该将每台设备每次发生故障的时间进行记录,然后在一定时间周期内进行平均计算,计算出其故障平均间隔时间。但实际上,在企业内或者产线内,设备台数太多,如果每台设备每次都进行计算的话,统计量太大,除非有相关智能装置,否则难以统计。考虑到这一实际状况,所以一般计算时,采用以下计算公式进行计算。
MTBF=稼动时间÷Σ故障次数
例:某条生产线一个月的稼动时间为:8小时/天×22天/月=176小时/月,这个月共发生故障了10次,那么该产线的MTBF=176小时/月÷10次/月=17.6小时。
MTTR的计算方法
MTTR故障平均恢复时间,也就是从故障开始到故障维修完成的平均时间。
其计算公式如下:
MTTR=Σ故障时间/Σ故障次数
例:某条生产线一个月的总故障时间为20小时,共故障了10次
则:MTTR=20小时÷10次=2小时/次。
为什么要分析MTBF?
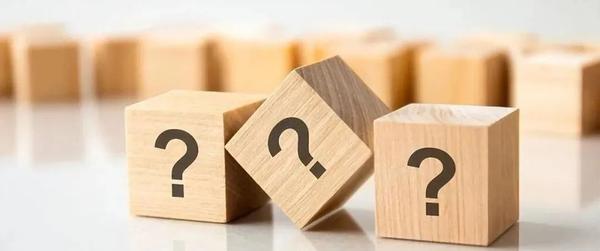
MTBF是衡量设备维修及保养效果的指标。如果MTBF值越大,则说明其设备维修和设备保养效果更好。如果MTBF能达到1个月时间,那么以后的设备保养周期就可以设置为1个月,每次保养完成之后,到下次保养期间就可以不用进行设备维修和保养维护,这样的生产过程稳定性就非常好,生产效率也高。
(1)提升MTBF是企业所有人员的需求
提升了MTBF,对公司整体来讲,生产过程就会比较稳定,生产效率高,那么公司效益当然就好;同时,对于设备维修人员来说,工作量就会大大减少,工作清闲。
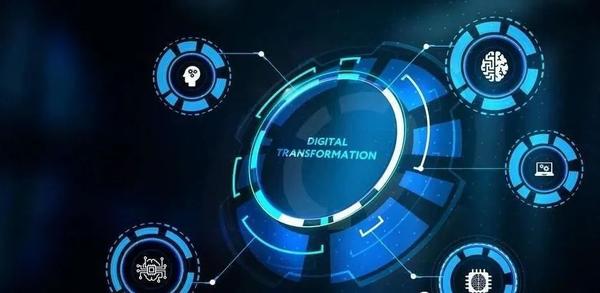
(2)提升MTBF是未来企业状态需求
未来的企业一定是无人化的智能工厂,也就是我们常说的黑灯工厂。
黑灯工厂在日常生产过程中是没有人的,是自动进行的。那么,如果设备发生了故障,就无人人去处理,生产过程只能被迫停止。
所以基于以上两点,设备维护和保养人员应该不断地追求MTBF指标的提升。
看到这里,肯定有人会说怎么可能,设备毕竟是由一个个零部件构成的,其在运转过程中一定会存在磨损、精度损失等问题,怎么可能会实现无人化的生产过程?
对于这个问题,大家可以转化下思维,虽然设备一定会发生故障,但在一定时间周期内难道就不能实现0故障吗?既然设备是由一个个零件组成,那么每一个零件都是有其寿命的,只要对各部件的寿命和使用条件进行严格把控,那么在各零部件寿命周期内就可以不发生故障。
无人化的黑灯工厂现在已经在很多企业实现,如我国的宝钢、韩国的浦项等大型企业中,已经完全实现了无人化的黑灯工厂。
4、为什么要分析MTTR?
MTTR是衡量设备维修效率的指标。MTTR值越小,说明维修人员的工作效率越高,同时也说明维修保养人员的工作技能越好。
所以要不断对MTTR进行研究、分析,并制定改善措施进行改善,以提升工作效率和人员的工作技能,最终使企业运营效率提升。
一般一个故障维修过程如下图所示:
设备维修从大的方面来看主要由三个阶段构成,分别是事前准备阶段,维护保养阶段和结果确认阶段。其中事前准备阶段又包括信息收集、分析判断、工具准备和人员移动几个过程。
事前准备阶段和结果确认阶段实际上是无价值劳动,应该要极力压缩,甚至要朝着0时间去改善。
在很多人的认知中,维修保养时间占据绝大部分的时间,但经过统计,往往很多时候是事前准备时间远远高于维修保养时间。这个认知偏差主要是因为大家没有对这些时间进行仔细统计和区分。
举一个简单的示例来说明。在某大型钢铁企业,有一天凌晨5点钟,一台大型设备发生了故障,该设备是由外协单位进行保养维护的。
故障发生后,设备操作人员立即提报了故障维修需求。到了早晨8点钟上班后,外协单位派了一位维修人员到现场了解情况,到了现场后,现场操作人员告知是电路故障,而该维修人员属于机械专业的,因此不能判断,打道回府,回了办公室。
这时候已经到了8点30分,然后又派了另外一名电气维修人员到现场了解情况,了解到可能是某个电容烧损的信息,由于未携带任何工具,因此又回到了办公室。
到了9点钟左右,再次带着万用表等工具到现场进行测量分析,测量分析后发现是一个电容损坏,然后又回到办公室拿取电容。等找到电容,拿着维修工具再次来到现场,时间已经到了上午10点钟左右,经过大约10分钟的维修和20分钟左右的试机,本次故障终于维修完成。
这整个过程中,维修准备时间整整花去了300分钟,占总时间的91%;而维修时间仅10分钟,占总时间的3%;效果确认时间也仅20分钟,占总时间的6%。
再看下另外一家企业,该企业是一家世界排名第二的日本轴承生产企业,该企业之前的维修准备时间平均大约需要30分钟左右,后来经过他们的分析和改善,最终将维修准备时间压缩至5分钟,并将5分钟定为维修人员的一个考核项,也就是从接到故障维修需求到现场开始维修时间仅需5分钟。5分钟对比300分钟,多么可怕的差距。
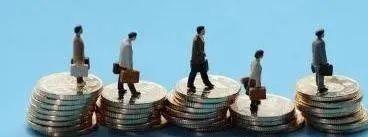