一、标准工时的定义
所谓的标准时间,就是指在正常条件下,一位受过训练的熟练工作者,以规定的作业方法和用具,完成一定的质和量的工作所需的时间。标准时间的界定条件:①规定的环境条件下②按照规定的作业方法③使用规定的设备、治工具④由受过训练的作业人员⑤在不受外在不良影响的条件下⑥达成一定的品质要求二、标准工时的制定步骤
1、工艺拆解:将现场所涉及到的所有工艺进行统计和划分,然后将每项工艺的加工步骤进行拆解。2、明确工时测定的方法,进行工时的测定与记录:a. 选择合适的员工-取得上岗证,并且在理解图纸,做好所有产前准备工作,再进行测时;b. 运用秒表测量法测定工时。操作者连续生产五件产品,记录从拿起第一件产品一直到放好最后一件产品的时间,再其取均值,记作单个零件的加工时间。计划人员可依据此结果,将每个产品的加工工艺及工艺拆分进行结合,计算每类产品的加工标准工时。3、将各工艺的标准工时测定结果进行求和,即为该产品的标准工时,依据该产品订单数量、车间排班、宽放率等进行生产计划的下达,可大大提高生产计划的指导性。
三、标准工时的制定方法
1、直接测时法(包括:秒表法,影像法)2、间接测时法(包括:预定工时法,标准资料法)我们对这4种方法将对其优劣之处,使用场合进行分析:(一)直接测时法:此方法一定要在有实际生产的情况下,才能测定工时,适合于量产产品的现场改善。1、秒表法优点:应该可以说这是四种方法中最简单快速、实施成本最低的方法。缺点:假若操作单元时间都非常短,那么测量的人员也是反应不过来的,这样数据就产生了问题。另外,此方法缺少二次分析、追溯的能力,因为记录下来的仅仅只有一个数字而已。建议使用场合:量产阶段。一般可以用来测量每个工位周期时间,绘制线平衡图表,可进行人机作业分析。由于测量精度问题,不建议测量周期时间较短的工位,不建议将数据进行双手作业分析,不建议据此生成标准资料。2、影像法(视频法)优点:这种方法是我见过使用率最高的方法。它的精度相较于秒表法会更高,由于视频的存档,它具备二次分析、追溯的能力。缺点:但是它的问题就是分析的低效:很多公司使用视频剪辑软件对视频进行分割,从而获取操作单元时间。因为不是专门的分析软件,所以整个分析过程痛苦无比,费时费力。原文链接的软件可以解决这个问题。建议使用场合:量产阶段。几乎可以运用所有的场合。注意精度需求和分析精度之间的权衡。(二)间接测时法:此方法在没有任何实际生产的情况下,能够获得标准工时,适合新产品的规划。3、预定工时法优点:具体的方法有:MTM,MOST,MOD。它们最大的优点就是不需要实际生产。另外,预定工时法的分析结果可以作为一个改善的基准。缺点:必须对每个编码的起始点,结束点,包含动作了如指掌。否则很可能产生遗漏了某个工作导致预定工时分析出来的工时偏短。另外,如果长期使用预定工时法会导致疏离工厂现场,导致分析结果脱离实际。建议使用场合:新产品导入阶段、量产阶段。要注意编码假设环境与现实环境是否相同。4、标准资料法优点:利用企业历史信息进行快速制定标准工时。并且由于是企业本身产生的历史数据,所以标准工时更加准确,同时,通过该历史数据中设定改善目标,也更加具备可实施性。缺点:标准资料库不是一朝一夕就能形成的,需要企业不断地从上述几种测量方法中总结提取,形成标准资料库。因为总是有新产品和新工艺出现,所以需要不断的进行补充改善。建议使用场合:新产品导入阶段、量产阶段。几乎可以运用所有的场合。注意历史数据所在环境与现在数据所在环境是否相同。四、标准工时的计算
标准时间=观测时间×评比系数×(1+宽放率)=正常时间×(1+宽放率)
①观测时间:是实际观测得到的时间值的平均,而观测时间由于受到作业者熟练度、工作意愿、情绪等的影响,并能代表真实的情况,故此应加以修正,乘上一定的评价系数,求得实际时间作为标准时间的主体,另外,实际时间还应考虑一定的宽放,这样才得到标准时间。
②评比系数:评比是一种判断或评价的技术,目的是将实际的操作时间调整到平均工人的正常速度。其中影响评比的因素包括:操作者的熟练程度、设备工具的完善度、操作者的教育程度、工作的困难度等例:以100%作为正常速度的基准,如果评价系数为1.1(即110%),代表比正常速度快10%左右,如果评价系数为0.6(即60%),由代表作业速度相当于正常速度的60%。
③宽放:宽放是指由于管理需求、生理需求、疲劳等不可避免的因素而给予标准工时制定调整的一个方法。宽放率=(标准工时-实测工时)/实测工时*100%=管理宽放率+生理宽放率+疲劳宽放率宽放率主要是如下几个方面的总和:管理宽放一般取3%-10%;生理宽放一般取2%-5%;疲劳宽放一般取5%-20%;特殊宽放。五、标准工时的用途
在生产型企业中,标准工时的测定工作十分重要。由标准工时可以评估工厂、产品、工序和设备的标准生产能力,从而预估产品的交期和新产品开发所需的时间成本;是生产成本、产品定价和报价的数据来源之一;是人机配合、生产线平衡计算的重要参考;是生产计划制定、调度进行排产、生产要素配置和生产进度跟踪的重要依据;另外,根据已知的标准工时、员工作业时间和工作量可计算出每位员工的作业负荷率,它还是员工绩效考核和作业指导训练的重要标准。因此测定标准工时成为许多工作开展的前提和基础。六、工时测定不准确的原因
①测时人员的工作态度不端正,不重视工时测定的工作,不经测定就凭经验估算工时,应付差事;②测时人员的素质水平参差不齐,测时的方法和标准不统一。七、关于测时的注意事项
①首先要明确划分出加工工序以及工艺,分别明确不同产品加工的起止步骤分别有哪些,在测量出总时长的基础上,再分别测出每个分解动作所需的时间,在检验数据的准确性时,可以将每个动作所需的时间相加,与总时长相等即可;
②测时的过程中,要减掉为了加工产品所做的准备动作,如换模、调试的过程等不应计入到标准工时以内;
③另外,在计算工时之前,要去掉作业工时数据中极高和极低的异常值,然后再取平均值;
④由于设备异常、违规操作等因素影响而导致不合格品生产的工时,不能作为标准工时的参考数据,因此,首件产品的加工时长通常不会计入到测算范围内,因为首件产品的质量常常具有不稳定性。测时人员应该在产品生产过程中随机连续地选取若干(≥5)件产品(首件除外)的生产时间进行测时,即记录从拿起第一件产品,到放好最后一件产品的时间,再其取均值,记作单个零件的加工时长;
⑤要在不同的时间段,经过多次测量,算出均值,从而得出标准工时,由于作业的时间段不同,员工的疲劳程度、作业环境的光线和天气是不同的,人员的作业时间和效率也会因此有所差别;
⑥要选取若干个有经验的熟练员工来进行标准作业平均时间的测算,某个工序可能存在若干个作业人员,但由于技能水平和熟练程度不同,作业时间会存在差异,此时要以熟练工的操作速度为准;
⑦许多产品需要依赖设备进行加工,要对同一工序的若干件设备生产同种产品所需的加工时间分别进行测量,取得均值,来减轻因不同设备的老化和折损程度不同从而导致所需工时产生差异的影响;
⑧另外,测量工时的人员也要设置为多个,若仅安排一个专职人员进行标准工时的测定,很可能会因为测量人员的主观原因,导致测量数据缺乏准确性,要安排多个人员对同样的产品同时进行测时,评估其所测数据之间是否存在巨大的差异。
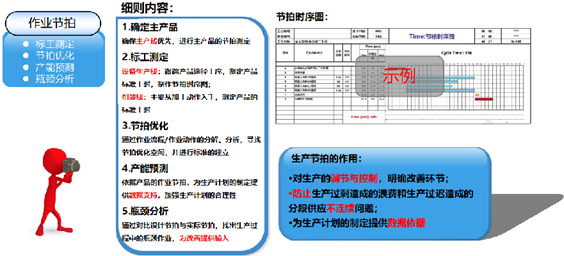
所谓生产节拍Take time,是指生产一个产品所需的时间,即一天的工作时间除以一天所生产产品的数量。这里一天的所需生产数量是根据生产计划来确定的,而生产计划是基于市场预测和订单情况制定的。因此,每天的生产数量并不是一定的,而是不断变动的。精益企业要求每一个人都使用标准工作程序、用与客户需求的速率take time相匹配的节拍生产产品。生产节拍不一定等于生产周期。如果生产周期大于生产节拍,就需要安排加班,或提前安排生产,储备一定库存,以满足生产节拍的需要,无论是加班和增加库存都需要增加成本;如果生产周期小于生产节拍,则产能过剩。两种情况都会产生浪费。因此,在组织同步化生产过程中,要尽量追求生产周期与生产节拍的基本一致。通过生产节拍的控制,可以平衡生产中各种资源运动的量与速度,识别并解决生产中的瓶颈问题。因为①设备等的硬件的更新迭代,产品的加工效率提高;②产品的工艺路线优化调整,需要重新产品工艺卡;③人员作业工作分析及作业标准化等各方面动因会造成节拍变更,需要对节拍进行重新测定,并对比变更前后的标准工时,以此来评判节拍优化的效果。案例:
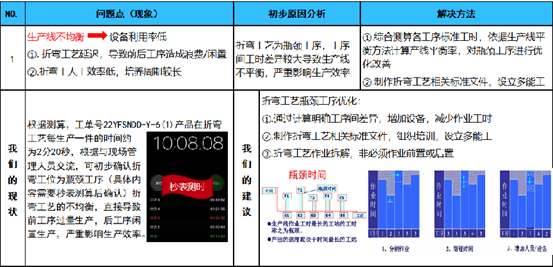
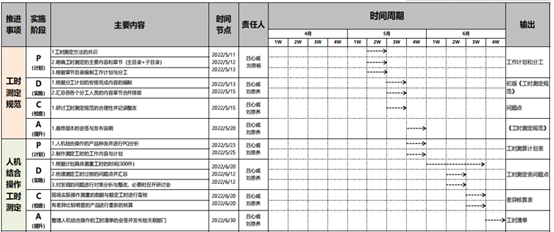
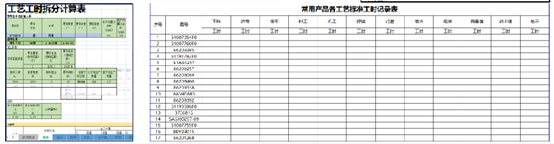
爬坡曲线设计标准的节拍,标准的动作组成每个标准工位的工作周期。结合人因工程中疲劳宽放、生理宽放和学习曲线等因素,为新产线和切换产线的爬坡做合理设计。
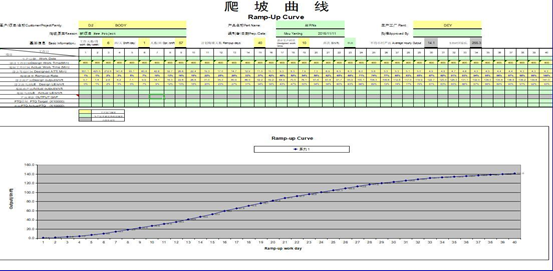
1>基础工艺划分:将现场所涉及到的所有工艺进行统计。
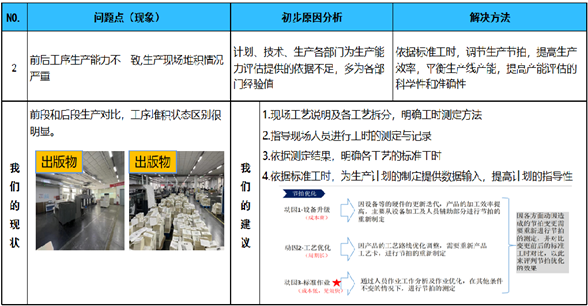
2>工艺拆解:将每项工艺的加工步骤进行拆解,分为人工作业及设备作业。
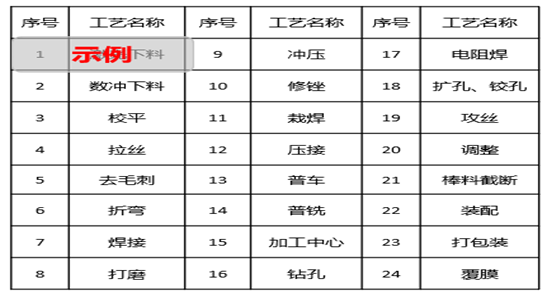
3>工时测定:人工作业-秒表测时法:a. 选择合适的员工-取得上岗证,并且在理解图纸,做好所有产前准备工作,再进行测时;b. 运用秒表测量法测定工时。操作者连续生产五件产品,记录从拿起第一件产品一直到放好最后一件产品的时间,再其取均值,记作单个零件的加工时间。设备作业-通用计划公式:(下图公式为案例)

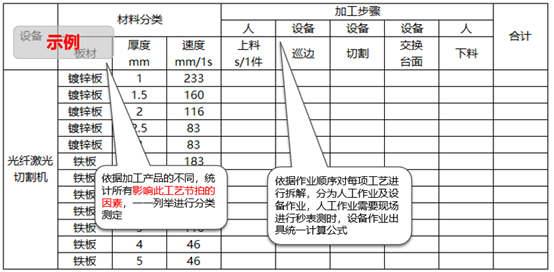
将每个产品的加工工艺及工艺拆分进行结合,计算每类产品的加工标准工时,即明确现场生产能力,同时了解客户需求,进行计划的精准制定。
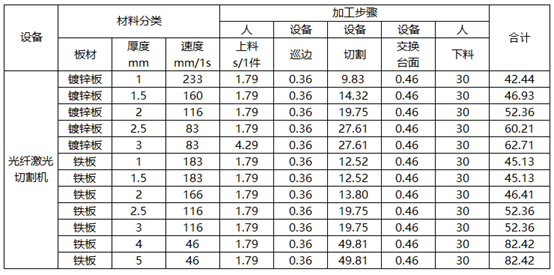
案例演示(以裁切工艺工时说明):a. 基础工艺划分
序号 | ① | ② | ③ | ④ | ⑤ | ⑥ | ⑦ |
工艺名称 | 裁切 | 印刷 | 烫金 | 折页 | 胶装 | 缝线 | 包装 |
a. 工艺拆解及工时测定(短时间内测定,数据存在不准确性)
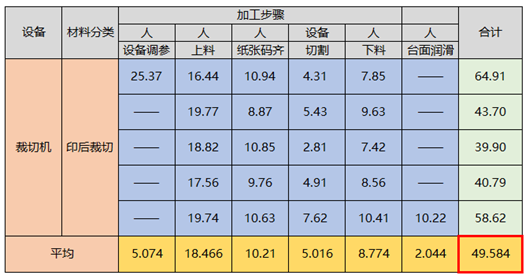
裁切的 标准工时 将每类产品的加工工艺进行划分,测定每个工艺的标准工时,求和即为该产品的标准工时,依据该产品订单数量、车间排班、宽放率等进行生产计划的下达,可大大提高生产计划的指导性。4>节拍优化
动因1-设备升级(成本高):因设备等的硬件的更新迭代,产品的加工效率提高,主要从设备加工及人员辅助部分进行节拍的重新制定。
动因2-工艺优化(周期长):因产品的工艺路线优化调整,需要重新产品工艺卡,进行节拍的重新制定。
动因3-标准作业(成本低,见效快)通过人员作业工作分析及作业优化,在其他条件不变的情况下,进行节拍的测定。因各方面动因造成的节拍变更需要重新进行节拍的测定,并对比变更前后的标准工时对比,以此来评判节拍优化的效果