很多企业在设备管理上都推行点检方法,但推行一段时间后的实际收效却不太理想,让不少强力推动者倡导者十分尴尬和被动。难道是设备点检方法本身有问题么?肯定不是,问题出在了推行点检的具体思路与做法上。
主要原因其实很简单:妄图一步到位,急功近利。为了达到这个目的,按照专家或教科书推行,起步高标准高要求,一开始就花大气力建团队、设标准、搞培训、立制度;狠一点的甚至直接要“政策”。
于是,文字和方案准备了一大摞,能落实到位的实质点检行动却有限。结果一段时间下来,千辛万苦制定的各种标准很多属于纸上谈兵并不实用,搞点检作业的维修工满腹怨气,点检效果自然也好不到哪里去,领导也没看到推行点检的明显效果。真所谓,希望越大失望越大。
其实按照《装备保障管理(CPM)》的观点,在工厂效益贡献并不明显的设备管理维修方面,搞任何变革或创新,都要从简单容易、快速有效的敏感点入手,尽量先低调小范围试点,待取得明显成效后再理直气壮的向上级要人要“政策”、大张旗鼓的甩开膀子大干。当然了,简单、有效、敏感点的选择是有技巧的,想必资深设备主管们都心中有数。
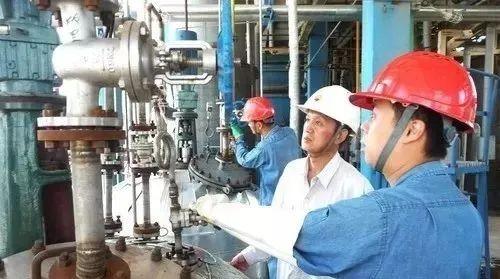
下面是一位老师傅整理的简单起步的点检要点,供同行朋友们开始推行点检时参考...
1.明确点检的目的
为了准确掌握设备的技术状况及劣化程度,对影响设备正常运行的关键部位进行管理制度化、操作技术规范化的检查维护工作称为设备点检。所谓“点”,是指设备的关键部位,通过检查些“点”,就能及时、准确地获取设备技术状态的信息。(点检对劣化倾向管理比较有效,重点在趋势预测上,随机性故障不应是点检的关注重点。)
2.简单实用的八定一成
定点:确定点检设备关键部位,薄弱环节;
定项:确定点检项目即检查内容(与技术水平匹配和仪器仪表配套,什么时代了,切莫拘泥于什么口眼耳鼻手方式);
定标:确定判断正常与否的标准(根据设备技术要求、实践经验);
定期:设定检查的间隔时间(主要依靠经验和重要程度);
定法:确定点检方法(需不需要解体?停机?用什么仪器(五感还是简单仪表)——一开始不要搞什么日常点检、精密点检的职能划分);
定人:确定检查项目的实施人员(最好实行专项专机专业负责,有利于发现异常);
定表:确定表单格式和记录要求(这个是必须的,只要对接到位,也是可以适当灵活的);
定流程:确定点检与维修的接口和工作流程(责权利要分清);
成闭环:步步落实,持续改进,闭环管理。
3.客观评价,切忌夸大其词
日本企业统计推行点检管理制度后达到了四个目的:
设备维修费用下降,幅度达到5%上,5年合计下降幅度达到20%特别好的一家工厂5年维修费用下降了30%,提高了企业劳动生产率,降低生产成本;
设备故障大大下降,故障率从平均1.5%下降到0.4%,突发故障发生次数下降了50多倍,需要抢修的突发故障下降了2倍多,故障停机时间下降了3.5倍;
计划维修比例上升,计划准确度提高,预防维修和计划工作按时完成率提高,计划维修项目提高3.5倍,非计划维修下降70%;
设备投资回报提高,设备可利用率提高25%。
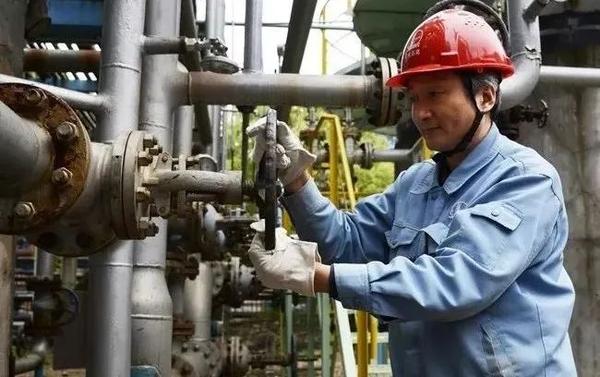
以下文章是一位设备员的发言稿,表达了其对设备点检的一些独特看法,特与大家分享一下。
一、我们为什么要选择点检制
设备管理在企业生产中占居非常重要的位置,企业的生产主要是人操作设备给我们生产出产品。因此,掌握设备的动态至关重要,掌握了设备的动态,下一步针对设备情况采取的措施将会是有的放矢。因为水平和经验的因素,也许刚开始的措施是不合理的甚至是错误的。但是只要用心,我们会很快迈上一个新的、更高的台阶。那么如何掌握设备的动态呢?途径很多,我认为就目前我们的现状,点检制是比较适合的。点检制搞好了,以后配以更先进的仪器仪表,就达到了在线检测。
点检制搞好了,我们在掌握设备的动态的情况下,逐步从“故障被迫性维修”向“预防性维修”转变。我曾经在设备主任的位置上干了五年,也有一些体会,最明显的就是你不知道什么难心事儿明天在等着你,维修工像救火队员一样到处扑火,你忙的团团转,领导的脸拉得老长,可收效又如何呢?我认为是负数,因为这么个忙法,你越忙对正常生产的影响就越大,生产效益就越差。过去曾经有种这样的说法:“我们的维修工越闲,说明我们的生产越正常”,我认为这也是不对的!这样会更进一步促使自己成为一个救火队员。
维修工在设备正常运转时必须有所为。
那么,他们做些什么呢?我认为要做基于点检制基础上的“预防性维修”,意思就是根据点检制基础上获取的信息,维修工有的放矢的提前做工作,在合适的时间实施维修。维修工在设备发现苗头到实施维修这段时间需要做材料备件准备、方案准备等,在实施维修前可以跟生产进行联系,使设备维修对生产的影响争取做到最少。我认为这就是推行点检制的目的所在,它最主要的好处就是让人处于有序状态,把工作做到前面,把影响降到最低。
二、我对点检制的一点认识
车间一把手必须要是推行点检制的坚强支持者
我是1997年到冶炼厂闪速车间参观学习时第一次接触点检制这个词的,当时觉得这挺好,就把人家的各种资料有意留着,想以后参考借鉴。但是,后来当设备主任时面对很多问题想推行点检制时,却因种种原因只好搁浅。直到去年我到提升工区,有这个条件了,另外,提升工区的实际情况也需要我们必须使设备管理的理念有个变化水平上个台阶。否则,人员少、任务重、安全性要求高、系统脆弱的现状根本无法满足矿里的出矿需求。
点检制是一个系统的工程,它涵盖车间管理的方方面面,它的推行涉及几乎所有人员培训、运作系统的设计等,它的运作涉及经济考核、生产跟设备的协调等。如果车间一把手不大张旗鼓的的推行,推行后不坚决维护它的运行,哪个人还能做成这件事?反过来,如果车间主任想做成这件事,有什么困难不能克服?
点检制不必是一成不变的模式
我们推行点检制前,参考了冶炼厂的一些做法,但是有区别。推行后又到选矿厂三选车间、二矿区西主井参观,发现每处都有不同。人家的东西不一定适合你,或者虽然好但自己的条件达不到。所以,只要保证点检制的本质意思不变,运行模式可根据自己的条件进行设计。适合的就是好的!
比方说点检卡我们是要求每班投到点检箱里的,而三选矿和西主井的是每月一本的;专职点检员人家每个车间都有五六位,而我们都是兼着别的职的。
所以,我们不必老考虑我们的条件达不到,只要冷静的分析我们的条件,一样可以设计出完全实用的点检体系。只要达到了为“预防性维修”提供准确可靠信息的目的、保证设备安全可靠运行的目的,就是好的!
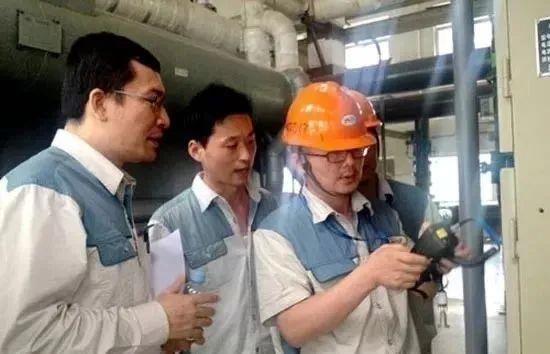
三、点检制给我们的回报是丰厚的
我们工区是从2006年4月份开始酝酿和准备,6月底开始正式推行点检制的。今年二月份,在装备部设备科技术人员的指导下,又进行了较大的修正和规范。从推行点检制以来,我工区共避免重大事故4起,发现隐患及存在的问题122起,设备造成的非计划性停车由2006年上半年的平均52小时/月降低到目前的20小时/月以下,目前各级点检均显示出了良好的运行效果。
从开始准备到推行的头几个月,我们感到确实很忙,本身的故障检修就够人受的了,还要憋着劲去做预防性维修。从一种体系转轨到另一种体系谈何容易,但我们憋着劲硬是挺过了转轨的阵痛。到去年十月份,基本完成了转型。
完成转型以后,车间管理者就比较轻松了。主要抓点检工作每个人是否尽到自己的职责,维修工的准备工作做得如何,判断和联系何时进行停机检修,根据判断当中的失误适时修改点检标准等。在此基础上,针对出现故障频率较高的地方进行技术改进,做到持续稳步地提高。这样就完全进入良性循环的轨道了。
总之,我认为推行点检制并基于此上的预防性维修,刚开始时挺累,最多半年步入正轨后,管理者虽然也做大量的工作但心不累了,管理高效了。
可见,点检制带给我们的回报是丰厚的!